Tactical backpacks are now hot on some e-commerce platforms such as Amazon, so many merchants are trying to enter this market. If you want to seize this opportunity, you first need to find a good tactical backpack factory to produce backpacks for you.
But many people do not know how to find a good tactical backpack supplier. When you are looking for a potential tactical backpack supplier, what questions should you ask them? Today I'm going to help you solve this mystery. I have listed 13 questions you need to ask a tactical bag factory.
The Tactical Backpack Factory Background & Experience
Key questions:
1.How long has your factory been in operation?
This question is very important. It gives you an idea about the experience, reliability and stability of this tactical backpack supplier.You can google the name of this vendor to get a feel for it. You can refer to my previous post:How to Find a Good Tactical Gear Supplier:Pro Tips & Tricks
Generally speaking, factories that have been operating for many years are likely to have perfected their manufacturing processes to ensure higher quality and efficiency. Experienced factories are more likely to have the expertise to handle complex or customized orders.
In addition, established factories are less likely to experience operational disruptions such as financial instability or sudden production shutdowns. This helps to ensure that your company is not faced with delayed production or unexpected supply chain issues.
As a general rule, my recommendation is that your tactical backpack supplier should be a factory that has been in business for more than 20 years.
2.Who are some of your major clients or brands you have worked with?
You can get an idea of a factory's standing in the industry by knowing which reputable customers or brands it has worked with. Factories with well-known repeat customers are more likely to produce quality products and maintain professional standards.
Big brands usually have strict quality and compliance requirements. If a tactical backpack manufacturer has worked with a well-known brand, it is an indication that they are able to meet high standards in production, materials, and quality control. This gives you confidence that they can deliver a top-quality product.
And their experience with a particular product or industry is reflected in the types of customers they have served. For example, if they have worked with outdoor or tactical brands, it shows that they are capable of producing tactical backpacks that meet industry requirements.
Production Capacity & Capabilities
Key questions:
3.What is your monthly or yearly production capacity?
If you know the backpack factory's production capacity, it will help you determine if they can handle the volume of orders you need. You need to make sure the factory has the capacity to produce enough tactical backpacks in the time frame you need if your business requires high-volume production.
You also can more effectively adjust your supply chain and distribution plans if you know the factory's capacity. It allows you to set realistic expectations for delivery times and ensures a smooth product launch.
4.Do you offer OEM((Original Equipment Manufacturer)/ODM(Original Design Manufacturer)services? Can you handle custom designs or branding?
This is a question you need to ask the tactical backpack factory. Because if you want to customize tactical backpacks with your own branding or unique design, OEM and ODM services can help you achieve that goal. This will help you stand out in the marketplace by ensuring that your product is distinctive and consistent with your brand image.
And when the bag factory can provide customization services in-house, it saves you the time and expense of hiring an outside designer or multiple vendors. From design to production, you work with one factory. This streamlines the process, ensures better coordination, and reduces production delays.
5.What materials do you typically use in your tactical backpacks?
The materials used in tactical backpacks have a significant impact on the durability, performance and overall quality of the pack. If you know the factory's material choices, it will help to ensure that the products are able to withstand specific conditions, such as waterproofing, abrasion resistance or impact resistance. You will then be able to assess whether they meet your standards and your customers' expectations.
Additionally, if you plan to offer customized tactical backpacks, knowing the supplier's typical materials can give you an idea of which ones can be modified or improved. With this information, you can discuss potential upgrades or changes to meet your specific branding or performance needs.
6.Do you have any certifications for quality management (e.g, ISO 9001)?
Certifications such as ISO 9001 indicate that a backpack factory adheres to internationally recognized quality management standards. This ensures that their production processes consistently meet high quality benchmarks, thereby reducing the risk of receiving substandard products.
Certification such as ISO 9001 ensures that the tactical backpack factory complies with global quality management principles, which is especially important if you plan to sell your products internationally. It also ensures that the vendor can meet any regulatory requirements in different markets.
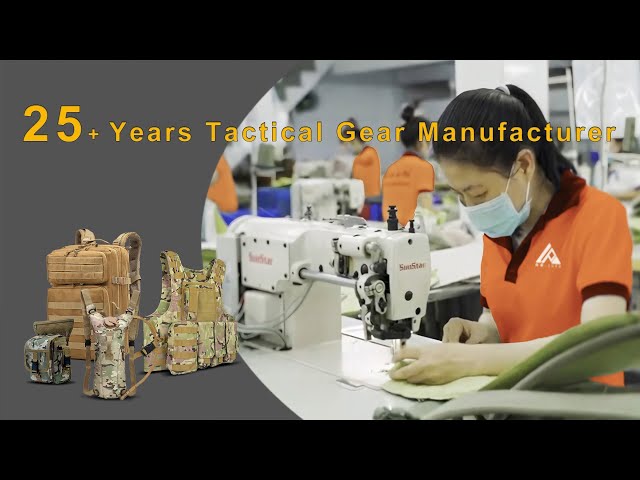
Quality Control & Standards
Key questions:
7.What quality control processes do you have in place during production?
Tactical backpacks are often used in harsh environments where poor quality products can lead to performance failures. By understanding a factory's quality control processes, you can assess their ability to produce a durable, reliable product that meets safety and functionality requirements, thereby reducing risk.
Factories with well-established quality control processes typically have more efficient production systems. This reduces delays, identifies problems faster, and speeds up order turnaround time so that market demands can be met more efficiently.
When a bag factory clearly outlines its quality control process, it demonstrates transparency and accountability. This allows you to monitor the production process more closely and ensure that they take the quality of your products seriously.
8.Can you provide product samples or a test batch before full-scale production?
You can inquire about and request samples of tactical backpacks. Receiving samples allows you to personally evaluate the quality of materials, workmanship, and overall durability of your tactical pack. This ensures that the final product meets your expectations and quality standards before going into mass production.
In addition, by testing in small batches, you can reduce the risk of discovering problems after mass production has begun. Identifying design or manufacturing issues up front can help avoid costly rework, delays or lost inventory down the road.
Lead Time
Key questions:
9.What is your typical lead time for orders?
The lead time for a batch of tactical backpacks is about 30-40 days.Understanding lead times helps you plan your business effectively. It allows you to align the ordering process with sales cycles, marketing campaigns, and inventory needs to ensure you have product when you need it.
If you know how long it takes factories to produce and deliver tactical backpacks, you will have enough inventory to meet customer demand. This helps you avoid out-of-stocks or backorders, which can damage your reputation and result in lost sales.
Inquiring about lead times also lets you know about other potential delays, such as material shortages, holidays, or shipping times. This allows you to plan for the extra time needed outside of production.
Pricing & Payment Terms
Key questions:
10.What is your pricing structure for different order volumes (MOQ and beyond)?
You can manage your cash flow more effectively by understanding minimum order quantities (MOQ) and how pricing changes with order quantity. It ensures that you can place orders within your budget while still benefiting from economies of scale when ordering large quantities. Factories often offer discounts for large orders, and understanding pricing tiers allows you to negotiate better terms.
Also, if you're testing a new product or market, you may be able to start with a small order. Understanding MOQ and above MOQ pricing helps you balance the risk of committing to high volume production while keeping unit costs reasonable.
11.What are your payment terms (e.g, deposit, balance upon delivery, etc)?
Some factories may be flexible with their payment terms, depending on your order volume or the potential for a long-term relationship. By understanding their terms, you may be able to negotiate better terms, such as longer payment terms or reduced deposits.
For international orders, payment terms may include specific currencies or bank fees. You should know these details in advance helps you plan transaction costs and choose the best payment method.
Factory Audits & Site Visits
Key questions:
12.Can we schedule a factory audit or a visit to see your production facility?
A factory audit or tour verifies that the factory has the necessary infrastructure, equipment, and expertise to meet your production requirements. Seeing the backpack factory in person ensures that they are capable of producing tactical backpacks in the quality and quantity required.
During the tour, you can observe the supplier's quality control processes and determine if they follow the standards necessary to ensure consistent product quality. This helps you confirm that the factory is meeting the quality requirements you expect.
13.Do you allow third-party inspections during the production process?
Third party inspections provide an unbiased assessment of the manufacturing process and product quality. By allowing an independent inspector to examine the product during the manufacturing process, you can ensure that the tactical pack meets the standards you set before it leaves the factory.
Identifying quality issues early in the manufacturing process helps prevent defects in the final product. Third-party inspections can catch problems with materials, workmanship, or assembly early, reducing costly rework or returns after production is complete.